Systems
COMPANY OVERVIEW
Process Systems specializes Air Gas Liquid Drying Systems for the removal of condensates and water from liquid, gas, and air streams. We have designed systems for a wide range of operating pressures involving automated process controls, valves, and instrumentation; and we can provide field services on any equipment dealing with these applications.
CONSULTING
We also provide consultant services to analyze a specific application or problem and provide recommendations for improvements. We provide full field service capabilities on all types of absorption systems:
• Adsorption
• Gas Dryers
• Liquid Dryers
SERVICE
Process Systems specializes in servicing Kemp equipment and C.M. Kemp drying and adsorption systems. Process Systems has more than 25 years of experience in dealing with Kemp systems and manufacture’s systems. We can also provide service for other types of adsorption systems.
PARTS
Many adsorption systems, especially liquid dehydration, solvent dehydration and gas drying have engineered components. Process Systems can help in identify the specific component and help in sourcing new replacement components and parts for these systems. This is especially true for Kemp equipment parts. Kemp equipment is a specialized system and has been providing systems for over 40 years. Many of these systems are still in operation. Specialized components may need servicing or replacement. Many of these are no longer available. Process Systems can help in identifying and sourcing new replacements. In many cases we can eliminate the distributer or sales representative giving the customer a direct source for the replacement parts.
Many dryers have moisture analyzers to measure dew point. Many of these analyzers are old and some are obsolete. Process Systems is working with Cosa Brand Moisture analyzers. We have retrofitted a number to other analyzers with the Cosa Analyzer.
PROCESS CONTROL
Process Systems can help with retrofitting older controls with new PLC (Programmable Logic Controller) panels. Process Systems has retrofitted a number of older Kemp ORIAD dryers with upgraded PLC systems. Process Systems has also upgraded PPC DEA dryers with PLC systems.
Can upgrade exiting older controls with more up-to-date controllers. We can also add moisture analyzers to the new control systems to provide direct moisture indication and control. PLC systems provide an excellent platform to add a moisture analyzer, pressure transmitters and temperature elements to the control, thus eliminating mechanical switches in the control of the system.
Call today to learn more about how we can help your process systems.
REFRIGERATION
Mechanical air dryers use refrigeration to reduce the pressure dew point of compressed air. The dryers lower the temperature close to the freezing point of water - about 35°F-39°F - which causes the moisture in the air to condense out. The condensed liquid is taken out of the system with separators.
There are three kinds of refrigeration dryers; they are the direct expansion types: cycling and non-cycling and the chiller type.
The direct expansion model uses two heat exchangers. The hot compressed air transfers its heat in the first exchanger (air-to-air) to cooled, dry air that is leaving the dryer system. This first exchanger cools the inlet air and reduces moisture content. The inlet air then travels to a second exchanger (refrigerant-to-air), where additional heat is transferred to a refrigerant and the design dew point is achieved.
Three types of direct-expansion dryers are available. At low loads, the hot gas bypass type routes some of the hot compressed refrigerant from the discharge side of the compressor back to the inlet side. This re-heating action prevents freezing when the airflow is low. The thermostatic-controlled type of direct-expansion dryer shuts down under similar low-load/low-flow conditions. A thermal storage mass is utilized to continue cooling the air during refrigeration unit shutdown.
In the chiller dryer, the heat exchange is a two-step process. The hot, humid air is cooled by chilled water in one heat exchanger; and the now-warmed water is re-chilled by refrigerant in another heat exchanger.
Refrigeration dryers are best suited for higher dew point requirements, indoor applications where ambient temperatures are below 35°F and where low dew points are not a requirement.
Adsorbents remove the moisture from the air by attracting and holding the water to the surface of their particles, or by ion exchange using an Ion-Exchange Resin.
These systems can be broken down into two major categories:
- Heatless/Pressure Swing Designs-Open System
- Heat Reactivated/Convection Designs which can be divided into two
categories:
These types of systems can also be designed and adapted for any number of liquid dehydration systems.
These dryers use three types of Adsorbents:
- Activated Alumina
- Silica Gel
- Molecular Sieves
A fourth type for more specialized designs is Ion Exchange Resins, which come in various forms for a number of liquid and gas applications.
In a classic dynamic adsorption system, there are three distinct zones: the saturated zone which is in equilibrium with the incoming fluid, the mass transfer zone, and the active zone where no adsorption has occurred.
ABSORPTION
Typical absorbents are sodium chloride, calcium chloride, and urea tablets or beads. The deliquescent dryer that uses one or a combination of these expendable chemicals does not provide a fixed, outlet pressure dew point. Instead, the dew point varies directly with the dryer inlet temperature - the higher the inlet temperature, the higher the outlet pressure dew point. Thus, deliquescent dryers can be installed outdoors in combination with aftercoolers to prevent freeze-up in outdoor pipelines and equipment.
The outlet relative humidity depends on the inlet dew point. Typically, these dryers will lower the inlet dew point by 20 degrees. The calcium chloride tablets must be replaced on a regular basis, as they dissolve in contact with the water in the compressed air to form a brine solution that must be drained and disposed of.
This type of dryer was popular at one time because of the low capital cost compared to other dryers at the time. Although this type of dryer will reduce the dew point, it cannot produce a minus pressure dew point; and it has a tendency to contaminate downstream systems.
These dryers are still in operation, although we would not recommend this type of system for instrument or process air applications because of potential downstream contamination and poor dew point performance.
Absorbent chemicals used in air dryers are known as "deliquescent desiccants." They attract moisture by the chemical reaction known as absorption.
INTRODUCTION
All air, gas, and liquids contain moisture in various amounts up to saturation, where just a slight change in temperature or pressure can cause water to condense or cause problems in process systems.
The amount of moisture in the air (humidity) can be expressed in two ways. The first is in grains per cubic foot. A grain is a unit of mass. When the amount of moisture in a volume of air is so described, it is called "absolute humidity."
When the relative humidity reaches 100%, the air is holding all the moisture it can and is saturated. Any drop in temperature will cause the moisture to condense out of the air. This point, where condensation begins, is called the "dew point" of that particular quantity of air under those conditions of absolute humidity and pressure.
Moisture in liquid systems is typically expressed in parts per million. Solvents, just like gases, have saturation limits; and designs take these limits into consideration.
Process Systems, LLC can provide a full range of drying systems ranging from standard industrial designs to custom designed air, gas and liquid systems.
Following the links below will help in understanding the basics of air, gas and liquid dryers and hopefully aid in selecting the type of equipment you may need. We can help and guide in this process. We strive to be flexible in working with our clients to provide them with the best-suited system for their applications.
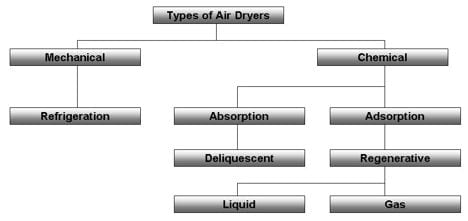
Relative humidity: Equals the ratio, expressed as a per cent of the weight of water vapor actually contained in a unit volume to the weight of water vapor which this same unit volume would contain if fully saturated at the same dry bulb temperature.
Absolute humidity: Equals actual weight of water vapor in the air at any given condition. Absolute humidity is usually expressed in grains per cubic foot or grains per pound of dry air (one grain equals 1/7000 pound).
Dew point: Equals the temperature of water vapor saturation of air, i.e., the temperature below which any further cooling would result in condensation of moisture from the air.
Water load doubles for every 10-degree rise in inlet temperature to an adsorption air dryer, which can double the size of the dryer.